صنعت فولاد یکی از صنایع کلیدی و حیاتی در هر کشور است و در ایران نیز باتوجهبه نقش مهم آن در تولیدات صنعتی و صادرات، توجه ویژهای به این بخش وجود دارد. یکی از چالشهای اساسی که صنایع فولادی با آن روبهرو هستند، تأمین انرژی لازم (برق و گاز) برای فرایند تولید است.
گاز طبیعی و برق، دو منبع اصلی انرژی برای تولید فولاد در کشور محسوب میشوند. با این حال در فصول خاص سال، کمبود این منابع میتواند تأثیرات جدی بر تولید و رقابتپذیری این صنعت داشته باشد.
کمبود برق در تابستان و مشکلات تولید فولاد
کمبود برق در تابستان میتواند به مشکلاتی همچون ناپایداری در فرایندهای تولید منجر شود که موجب اختلالات جدی در کیفیت محصولات نهایی میشود. تولید فولاد یک فرایند پیچیده و حساس است که هرگونه توقف یا نوسان در تأمین برق میتواند منجر به تولید محصولات معیوب یا کاهش کیفیت آنها شود.
بهویژه در فرایندهای حساس مانند ذوب و ریختهگری، نیاز به تأمین برق مستمر و با کیفیت بالا وجود دارد. هرگونه وقفه یا اختلال در این فرایندها میتواند موجب آسیب به تجهیزات گرانقیمت و آسیبدیدگیهای فنی دیگر شود که هزینههای تعمیرات و نگهداری را به طور چشمگیری افزایش خواهد داد.
همچنین، کاهش تولید به دلیل کمبود برق میتواند بر تأخیر در انجام تعهدات صادراتی و کاهش درآمدهای ناشی از فروش فولاد در بازارهای جهانی تأثیر منفی بگذارد. کاهش ظرفیت تولید بهویژه در دوران تقاضای بالا در بازارهای بینالمللی، باعث میشود که صنایع فولادی ایران نتوانند بهموقع و به مقدار کافی محصول تولید کنند و در نتیجه، بخش بزرگی از بازارهای صادراتی خود را از دست دهند.
این کاهش درآمدها میتواند منجر به مشکلات مالی برای تولیدکنندگان فولاد و تضعیف جایگاه رقابتی آنها در بازارهای جهانی شود. در نتیجه، تأمین برق پایدار و کاهش وابستگی به منابع انرژی فسیلی در تابستان باید به یکی از اولویتهای اصلی صنعت فولاد تبدیل شود تا این مشکلات کاهش یابد.
کمبود گاز در فصل زمستان و تأثیر آن بر صنایع فولاد
علاوه بر مشکلات مرتبط با توقف یا کاهش تولید کمبود گاز در زمستان میتواند به اثرات بلندمدت منفی بر فرایندهای تولید فولاد و زیرساختهای کارخانهها منجر شود. کاهش تأمین گاز ممکن است باعث شود که واحدهای تولیدی به روشهای جایگزین و ناکارآمد برای تأمین انرژی متوسل شوند که این امر میتواند موجب کاهش کیفیت محصولات و افزایش خرابیهای ناشی از استفاده غیربهینه از تجهیزات گردد.
تولید فولاد بهشدت به گاز طبیعی برای فرایندهای ذوب نیاز دارد و در صورت عدم دسترسی به این منبع انرژی، واحدهای تولیدی مجبور به کاهش ظرفیت یا توقف کامل فرایندهای تولید خواهند شد که این امر به طور مستقیم بر میزان تولید و سودآوری کارخانهها تأثیر میگذارد.
در شرایط کمبود گاز، صنایع فولادی باید هزینههای اضافی برای خرید گاز با قیمتهای بالاتر یا استفاده از سوختهای جایگزین را بپردازند. این افزایش هزینهها به طور مستقیم به قیمت نهایی محصول فولاد منتقل میشود و در نتیجه توان رقابتی فولاد ایران در بازارهای بینالمللی کاهش مییابد.
همچنین مشکلات تأمین گاز میتواند به تأخیر در انجام تعهدات صادراتی منجر شود و ایران که یکی از تولیدکنندگان عمده فولاد در منطقه است نتواند بهموقع سفارشهای خارجی را تأمین کند که این امر ممکن است منجر به ازدستدادن بازارهای کلیدی صادراتی و کاهش سهم بازار ایران در رقابتهای جهانی شود.
افزایش هزینه انرژی و تأثیر آن بر رقابتپذیری صنایع فولادی ایران
یکی از چالشهای مهم دیگر برای صنعت فولاد ایران، افزایش هزینه انرژی است. باتوجهبه نوسانات قیمت انرژی و کمبود منابع گازی و برقی در کشور، صنایع فولادی با افزایش چشمگیر هزینههای تولید روبهرو هستند. این افزایش هزینهها تأثیر مستقیمی بر سودآوری صنایع فولادی و توان رقابتی آنها در بازارهای جهانی دارد.
به طور معمول در بازارهای بینالمللی، رقابت میان تولیدکنندگان فولاد بسیار شدید است و صنایع باید هزینههای خود را به حداقل برسانند تا بتوانند محصولات خود را با قیمت رقابتی عرضه کنند. افزایش هزینه انرژی بهویژه در ایران که بخش عمدهای از تولید فولاد به مصرف انرژیهای فسیلی وابسته است این رقابت را برای تولیدکنندگان داخلی دشوارتر میکند.
از سوی دیگر افزایش هزینههای انرژی میتواند موجب افزایش قیمت فولاد تولیدی ایران در بازارهای صادراتی شود که این امر باعث کاهش تقاضا و ازدستدادن سهم بازارهای جهانی میشود. در نتیجه رقابتپذیری فولاد ایران در سطح جهانی با چالشهای بیشتری روبهرو خواهد شد.
پیشنهادهایی برای مقابله با بحران تأمین انرژی در صنعت فولاد
سرمایهگذاری در منابع تجدیدپذیر مانند انرژی خورشیدی و بادی ، توجه به تکنولوژیهای نوین در تولید انرژی و بهرهبرداری بهینه از منابع ، بهکارگیری سیستمهای هوشمند در مدیریت مصرف انرژی میتواند به طور قابلتوجهی به کاهش هدررفت انرژی و بهبود عملکرد تولید کمک کند.
برای مثال استفاده از سیستمهای کنترل اتوماتیک که بهصورت دقیق و بهموقع مصرف انرژی در کارخانههای فولاد را تنظیم کنند میتواند موجب کاهش مصرف بیرویه و بهینهسازی فرایند تولید شود. علاوه بر این بهکارگیری فناوریهایی مانند “اینورترها” برای کنترل دقیق سرعت موتورهای الکتریکی و استفاده از “سیستمهای ذخیرهسازی انرژی” برای زمانهای پیک مصرف میتواند به کاهش هزینهها و بهبود کارایی انرژی کمک کند.
همچنین افزایش آگاهی و آموزش کارکنان در کارخانههای فولاد در خصوص بهینهسازی مصرف انرژی میتواند نقش مهمی در کاهش هزینهها و بهرهوری انرژی ایفا کند. ایجاد فرهنگ مصرف بهینه انرژی در سطح کارخانههای فولادی و آموزش تکنیکهای ساده همچون خاموش کردن دستگاهها در زمانهای غیرضروری و استفاده از تجهیزات با بهرهوری بالاتر میتواند به طور گستردهای به کاهش هدررفت انرژی کمک کند. در این راستا دولت و صنایع باید به طور مشترک برنامههای آموزشی و کارگاههای آگاهیبخشی را برای مدیران و کارکنان صنایع فولادی طراحی و اجرا کنند. این اقدامات میتواند تأثیرات مثبت بلندمدتی در کاهش فشار بر منابع انرژی و بهبود وضعیت تولید فولاد در ایران داشته باشد. این اقدامات نهتنها مصرف انرژی را به حداقل میرساند بلکه موجب کاهش فشار بر شبکههای برق و گاز کشور نیز خواهد شد.
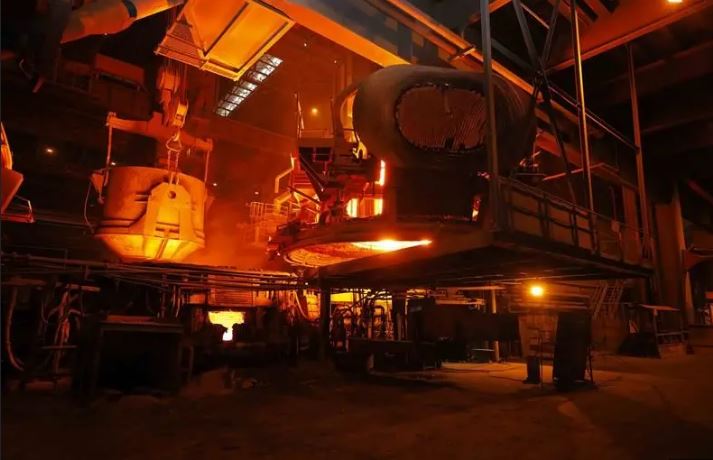
منبا: گروه بازار خبرگزاری علم وفناوری آنا
برای اطلاع از به روز ترین اخبار فولاد، وب سایت شرکت سامان کار ویرا (سکو) را دنبال کنید.